Higher efficiency of heat transfer systems demands higher heat fluxes, smaller packages and more efficient use of materials, hence optimal design of thermal systems such as heat exchangers and regenerators becomes increasingly important.
At the same time advanced manufacturing techniques such as powder metallurgy and additive manufacturing techniques make realization of complex geometries practical and economical. The TOpTEn project combines state-of-the-art modeling and topology optimization (TO) techniques with state-of-the-art manufacturing techniques to provide systematic design techniques for complex multiphysics heat transfer systems. Potential applications are numerous but the project focusses on three main applications: single phase heat sinks, thermal regenerators and thermoelectric generators (TEG).
The overall goal is to further develop topology optimization (TO) as a design methodology for optimizing heat transfer performance in energy conversion systems. A secondary objective is to generate optimized structures for specific design conditions of each technology to be studied. The optimized structures will have enhanced heat transfer performance and e.g. reduced pumping power, which will allow regenerative devices and TEGs to operate at higher efficiency.
The optimized heat sink designs will result in more effective and even cooling of e.g. electronic components. Several selected designs for heat sinks and a TEG, will be fabricated using additive manufacturing techniques and compared experimentally to conventional designs in order to test the effectiveness of the developed optimization techniques. Finally, TO will be used to predict how variability in geometry due to manufacturing tolerances will affect the performance of the optimized structures and will be used to suggest designs that are less sensitive to small changes in geometry that can occur during manufacturing processes.
Project start: 01.09.2014. Project end: 31.08.2018.
The project will employ 4 PhD students and 2 Postdocs. The project is sponsoret by ” Det Frie Forskningsråds Sapere Aude-program – bevillings-ID: DFF – 4005-00320” (Danish Council for Independent Research).
Illustrations:
The design of thermal energy transfer systems is based on long-developed engineering intuition or trial-and-error approaches, possibly combined with simple parameter studies. This limits resulting designs to relatively simple geometries as shown in figure: 1. Heat sinks or passive coolers, e.g. for cooling of electronic components, mostly consist of one of two-dimensional regular ribs. Figure 2. Heat regenerators, which are very efficient types of heat exchangers, often consist of simple spherical particles ordered in regular or random patterns. The simple geometries listed may be straightforward to model, design and manufacture, however, according to the conjecture of the proposed TOpTEn project they are most likely not optimal and hence systematic design methods that allow full geometric freedom may improve their efficiency significantly.
Figure 1, Heat sink or passive cooler:
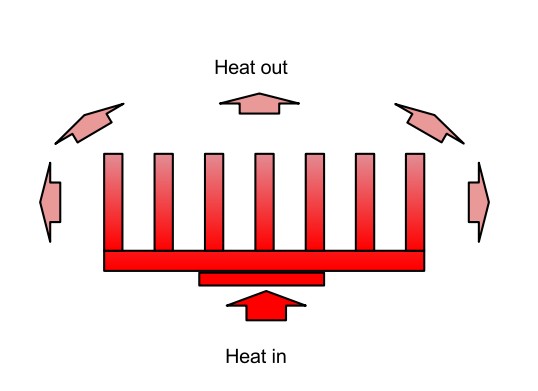
Figure 2, Heat regenerator:
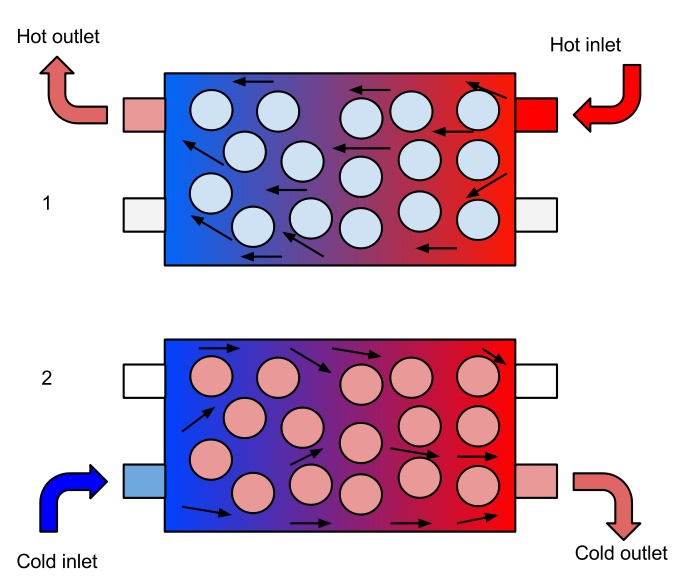